What Gas is Used for Mig & Tig Welding
Welding gas is an essential in both MIG and TIG welding and we use different types of gas depending on either the process and/or the material which we are going to be welding. Before we get into which gases are recommended for the which type of welding we should explain what the gases purpose is.
The gases role is to act like a shield around the arc, you will sometimes hear people refer to it as a shielding gas. It protects the weld pool from becoming contaminated from the surrounding atmosphere, i.e. we rely on oxygen to breathe however if this gets into the weld pool you will get something called oxidation which effects the strength and integrity of the weld. The gas also helps with maintaining a stable arc which ensures you are getting the best penetration into the material.
Now lets go through which gas is best for which purpose, we are going to keep this pretty simple and straight forward but it is worth baring in mind that you can really get scientific with all of this if you really wanted to.
MIG Welding
So for MIG welding, you are going to want a mixed gas. The mix is usually made up of argon and CO2 with some suppliers adding helium or oxygen to add extra assistance in keeping the arc stable. The best ratio to use would all depend on what thickness of material you would be welding and higher CO2 contents will be better for thicker materials. The most commonly used ratio is 95% argon 5% CO2 and is good for welding anything up to around 7mm thickness.
The only time you would use pure argon in MIG welding is when you would be using one of our spool guns for aluminum welding and other alloys.
TIG Welding
Pure argon is the only gas required for TIG welding. It doesn't matter what material you are welding or the thickness of the material, pure argon is your go to. If you try to introduce any co2 to a TIG weld, you would see the weld becoming a bit bubbly and black in colour.
An interesting fact about pure argon is that it is more environmentally friendly than other gases used in welding. It is becoming more and more frequently used now to reduce many companies impact on the environment.
Gas Tips
Correct flow rate - It is important that your flow rate is set correctly. An incorrect flow rate can result in imperfections in the weld, damage to the tungsten if TIG welding and an a waste of gas. We suggest using a flow meter to really fine tune the rate.
Black Tungsten - If you notice your tungsten is going black at the end, you do not have the correct gas coverage shielding the arc. Up your flow rate and see if this makes a difference.
To Much Spatter - When MIG welding, if you notice a lot of spatter, it may be the lack of gas causing the issue. Up the flow rate and maybe consider a gas with a higher CO2 content. If everything with the gas is fine, check your wire speed and voltage settings.
Gas Rush - What we mean by this is that when you first pull the trigger on the torch, you get a huge rush of gas. We suggest just cracking the tap on the bottle open and adjusting the gas rate through the regulator. By doing this, you should minimise that initial rush of gas.
Welding Outside - Try to avoid this the best you can. The slightest breeze will blow away your shielding gas rendering it absolutely useless and a waste. You can get a flux cored wire for gasless MIG welding. We advise against TIG welding outside unless you are able to shield yourself from any breeze.
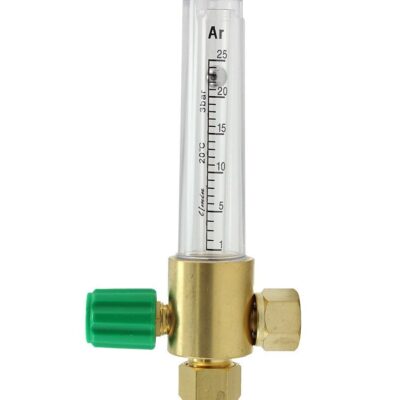
New to MIG welding? Read MIG Welding Tips & Tricks