R-Tech P31C Plasma Cutter - What Changed?
It's been no surprise to us how popular the R-Tech P30C Plasma Cutter has been. The small, compact and reliable machine has been put through its paces in thousands of workshops, garages and sheds across the UK and Europe and still remains a heavy contender in the small plasma cutter market.
But if its so popular, why change it?, Don't fix what isn't broke... right?. Well, the P30C has remained the same for years and as those years have passed, new, updated, technology has been released so it made sense to give the machine some more of the love and attention it deserved.
So, what changes were made whilst retaining the reliability and ease of use that customers have grown to love over the years?, lets take a look.
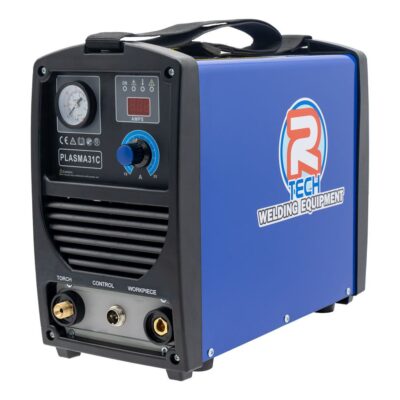
Air Filter, Water Trap
This has now been moved to sit within the machine rather than on the back. By moving this section, we reduced the overall length of the machine. This has made the machine more accommodating on work benches and trollies.
The filter can be accessed by a hatch we placed on the side panel of the machine to adjust the PSI. This also allows for easy draining of the filter, should you get any water within the lines. It's worth noting that this filter comes as standard with our R-Tech plasma cutters meaning you do not have the extra expense of sourcing an air line filter.
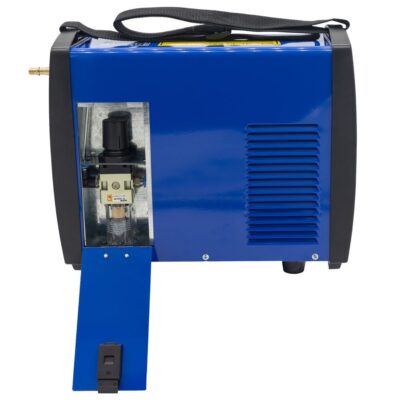
Front Panel
We have re-designed the front panel. Adding a couple more indicators so the machine provides you with more information when in use. An overheat warning light has been added along with a low air pressure warning indicator. When either of these are illuminated, the machine has either hit its duty cycle and needs to cool down or their is an issue with the compressor.
The test gas switch has now been removed as the gas can be tested by simply pushing down on the torch trigger whilst holding it away from the workpiece with the earth lead detached from the machine.
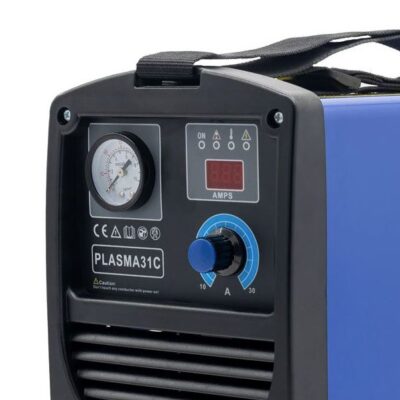
Internals
If you were to take the shell of the P30C, you would see that the machine consisted of 4 control boards that communicated with each other during the cutting process. This has now been reduced down to 1 main control board making it much easier to work on in the event of a fault.
Although the 4 individual boards were very reliable, the new control board has only boosted the machines reliability. This upgrade has also added more control over the amperage and therefore allows for more precise cutting.
For further information on this machine, please visit the R-Tech P31C Plasma Cutter Page.